Dem selektiven Schutz von elektronischen Bauteilen kommt angesichts der steigenden Anforderungen aus der Industrie und beim Endverbraucher eine immer größere Bedeutung zu. Im Hinblick auf die einfache elektrische Isolation und den Schutz gegen Korrosion mag ein Dünnschichtlack in vielen Fällen ausreichen. Zunehmende Herausforderungen, wie zum Beispiel der Schutz vor Vibration und extremen Umwelteinflüssen, können jedoch einen vollständigen Verguss von Baugruppen erforderlich machen.
Das Dam-and-Fill-Konzept bietet einen Kompromiss aus beiden Möglichkeiten und verbindet die Vorteile beider Verfahren, indem es einen selektiven Dickschichtlack darstellt. Eine Visualisierung der verschiedenen Schutzmöglichkeiten ist in Abbildung 1 dargestellt
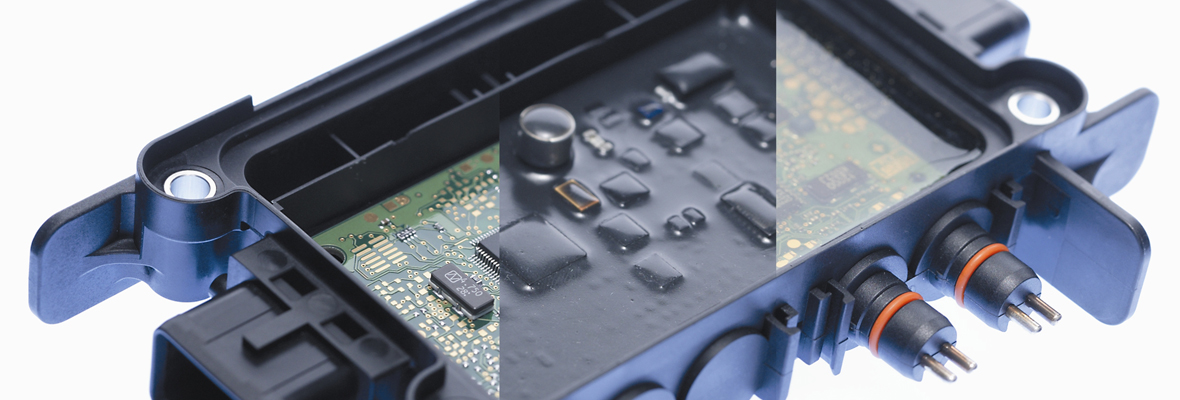
Die Grenze zwischen den jeweiligen Schutzmöglichkeiten ist dabei nicht klar definiert. Häufig werden Schichtdicken von weniger als 100 µm als Dünnschichtlack, bis 300 µm als Dickschichtlack und alles darüber hinaus als Verguss bezeichnet. Durch das Dam-and-Fill-Konzept können Schichtdicken von 100 µm bis hin zu 2 mm erreicht werden, weshalb wahlweise von einem Dickschichtlack oder Dünnschichtverguss gesprochen werden kann. Durch diese Art des Elektronikschutzes ist es möglich, die empfindlichen Bauteile nicht nur gegen Korrosion, sondern auch gegen mechanische Einflüsse und aggressive Chemikalien zu schützen. Der wesentliche Vorteil des Verfahrens gegenüber dem kompletten Bauteilverguss ist die mögliche Materialeinsparung.
Das Verfahren
Dam-and-Fill ist ein selektiver Prozess, der es ermöglicht, ausgewählte Komponenten auf der Leiterplatte (engl. Printed Circuit Board, PCB) zu schützen, ohne dabei die umgebenden Bereiche zu beeinflussen.
Dafür werden zwei Materialien mit unterschiedlichen Viskositäten genutzt. Ein hochviskoses Material wird zunächst als Raupe (Damm) um den zu schützenden Bereich aufgetragen. Anschließend wird die sich ergebende Vertiefung mit einem niedrigviskosen Material bis zur Bedeckung aller Bauteile oder bis zu einer gewünschten Höhe aufgefüllt. Abbildung 2 zeigt Detailaufnahmen von den einzelnen Schritten des Verfahrens
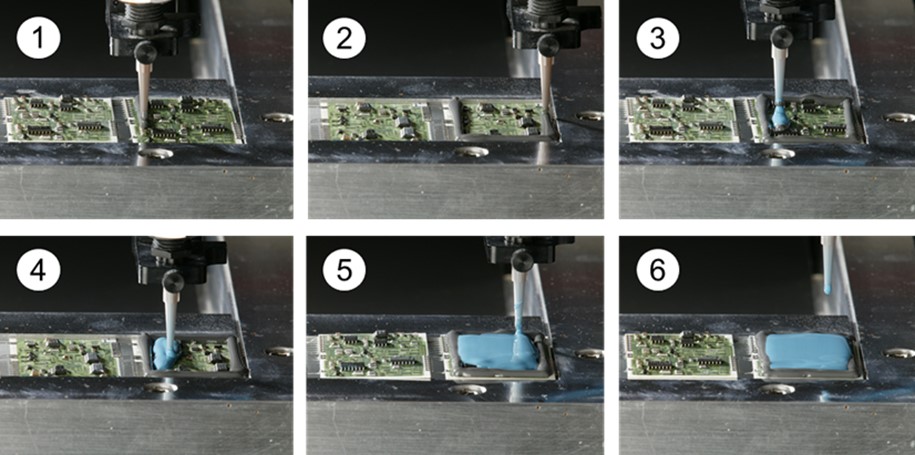
Typischerweise lassen sich so Schichtdicken bis zu 1 mm realisieren. Für besondere Anwendungen können höhere Schichtdicken erforderlich werden, da einzelne Komponenten andernfalls nicht ausreichend geschützt oder im ungünstigsten Fall gar nicht überzogen sind. In diesem Fall kann es notwendig sein, zwei Raupen übereinander aufzutragen, um so einen höheren Damm zu erhalten (s. Abbildung 3).
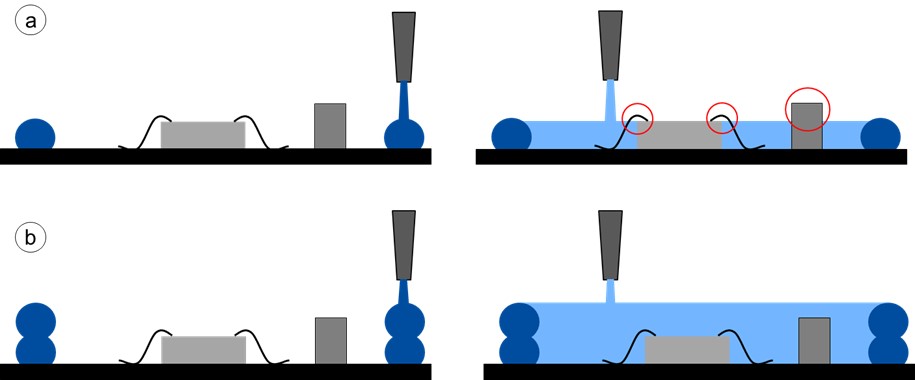
Das Legen des Dammes ist dabei ein wichtiger Schritt, der das Endresultat des Dünnschichtvergusses enorm beeinflusst. Das hochviskose Dammmaterial bildet die Barriere, die das niedrigviskose Füllmaterial in den ausgewählten Bereichen auf der Leiterplatte hält. Dementsprechend ist die Applikation des Dammes mit gleicher Höhe und ohne Lücken extrem wichtig, da es sonst zum Auslaufen des Füllmaterials kommt.
Rheologie des Dammmaterials
Die Rheologie des Dammmaterials ist ein wichtiges Qualitätsmerkmal für die Formgebung des Dammes. Die Viskosität der Dammmaterialien hat eine Bandbreite von etwa 30.000 bis 1.300.000 mPa·s. Durch das Fördern der Pumpe oder durch das Ausdrücken aus einer Kartusche kommt es jedoch zur Scherung des Materials und dadurch häufig zu einer Abnahme der Viskosität. Damit der Damm beim Auftreffen auf der Leiterplatte aber nicht verläuft, ist ein schneller Wiederaufbau der Viskosität von essentieller Bedeutung. Dieses auch als Thixotropie bezeichnete Verhalten wird durch spezielle Füllstoffe erreicht und macht eine Dam-and-Fill Anwendung überhaupt erst möglich.
Abbildung 4 zeigt das thixotrope Verhalten beispielhaft für zwei Chargen des Bectron® PT 4606. In Phase 1 der Messung wird das Material einer sehr niedrigen Scherrate (γ=0,5 s-1 ) ausgesetzt. In der zweiten Phase wird die Scherrate sprungartig erhöht (γ=12,5 s-1
), um so das Ausdrücken aus der Kartusche oder aus dem Dispenskopf zu simulieren. Es ist zu erkennen, dass die Viskosität durch die Erhöhung der Scherrate abnimmt. Dieses scherverdünnende Verhalten begünstigt zwar einerseits Förderung des Materials, gleichzeitig würde das Material mit so niedriger Viskosität beim Auftreffen auf der Leiterplatte jedoch verlaufen und keinen Damm mehr bilden. Somit ist ein schneller Wiederaufbau der Viskosität bei Reduzierung der Scherrate notwendig, was in Phase 3 ersichtlich wird. Bei einer Reduzierung der Scherrate auf γ=0,5 s-1
steigt die Viskosität wieder sprunghaft auf nahezu den Ursprungswert an, wodurch ein Verlaufen des Dammes verhindert wird.
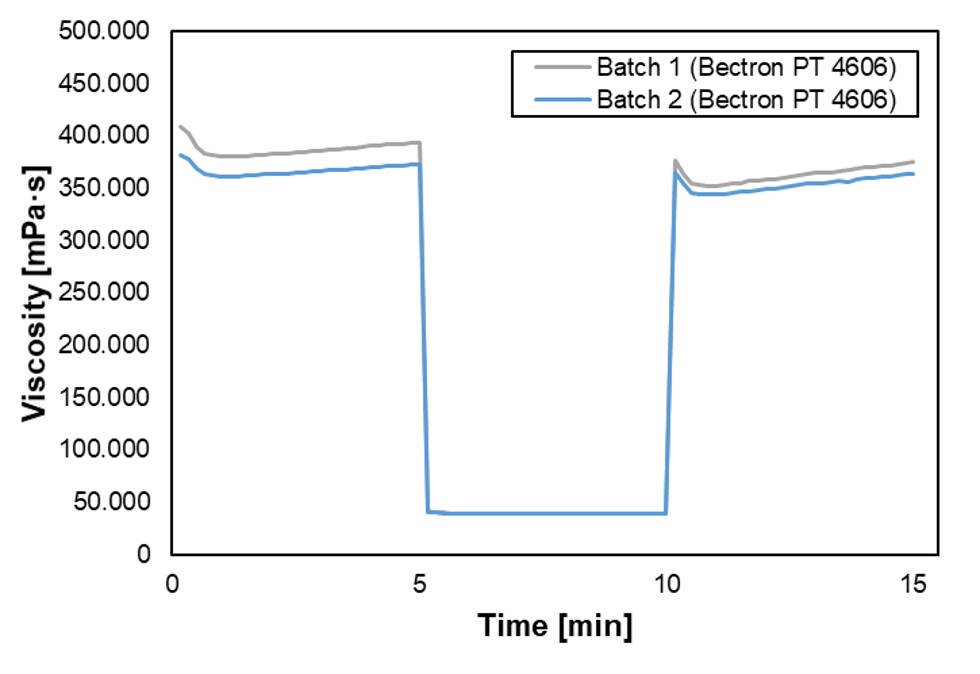
Speziell entwickelte ELANTAS Produkte
Aufgrund der vielfältigen Einsatzmöglichkeiten steigt die Nachfrage an Produkten für das Dam-and-Fill-Verfahren stetig an. Die ELANTAS Europe hat das Potential dieses Verfahrens bereits vor vielen Jahren erkannt und spezielle Produkte für diese Anwendung entwickelt. Das Resultat sind Produktreihen mit unterschiedlichen Eigenschaften, die für verschiedene Anwendungsfälle eine maßgeschneiderte Lösung bieten.
Bectron PT-Serie:
Bei der Bectron® PT-Serie handelt es sich um einkomponentige UV- und/oder feuchtigkeitsvernetzende Materialien, die auf einer Polyurethan/Acrylat-Chemie basieren. Die Produkte weisen eine gute Haftung auf vielen Oberflächen auf und überzeugen durch ein gutes Verhalten im Thermoschock von -40 bis +120 °C. Je nach Anwendungsfall und Bedarf kann der Kunde zwischen Materialien mit unterschiedlichen Härtungsmethoden wählen.
Bectron® PT 46xx sind Produkte, die sowohl durch UV-Strahlung als auch durch Reaktion mit Luftfeuchtigkeit aushärten. Die Härtung mittels UV-Strahlung dient dabei als schneller Härtungsmechanismus, der es ermöglicht, innerhalb weniger Sekunden ein stabiles Material zu erhalten, das direkt weiterverarbeitet werden kann. Gleichzeitig besitzen die PT 46xx-Produkte aber auch einen zweiten Härtungsmechanismus, der über die Reaktion mit Luftfeuchtigkeit funktioniert und die Aushärtung in den Schattenbereichen unter den Bauteilen sicherstellt. Dieser Mechanismus ist deutlich langsamer und dauert bei 3 mm Schichtdicke, 23 °C und 50 % Luftfeuchtigkeit circa zwei bis drei Tage.
Die Bectron® PT 48xx-Produkte sind von der Chemie und den Eigenschaften sehr ähnlich. Der Unterschied liegt in dem Härtungsverfahren. Die Bectron® PT 48xx-Serie härtet nur über die Reaktion mit Luftfeuchtigkeit aus. Die Feuchtigkeitshärtung ist aber deutlich schneller als bei der PT 46xx-Serie. Bei gleichen Bedingungen ist die Oberfläche bereits fünf bis sechs Stunden nach dem Applizieren klebfrei, so dass eine Weiterverarbeitung möglich ist. Die vollständige Aushärtung dauert circa 24 Stunden. Eine Übersicht der gängigen Bectron® PT-Produkte mit einer Einteilung nach Viskosität sowie Härtungsmechanismus und -zeit ist in Abbildung 5 gezeigt.
Bectron PK-Serie:
Bei der Bectron® PK-Serie handelt es sich ebenfalls um einkomponentige Polyurethan-Systeme, die thermisch härten. Das Besondere der PK-Produkte ist, dass der Härter in verkapselter Form mit dem Harz vorgemischt und anschließend durch die Einwirkung von Temperatur freigesetzt wird. Durch diese einzigartige Technologie kann Problemen mit einem falschen Mischungsverhältnis vorgebeugt und auf aufwendige Anlagentechnik zum Mischen von Harz und Härter verzichtet werden. Bectron® PK-Materialien sind lösungsmittelfrei und weisen eine niedrige Glasübergangstemperatur auf. Darüber hinaus zeigen sie gute Eigenschaften im Thermoschock von -50 bis +125 °C. Abhängig von den Anforderungen gibt es die eine Vielzahl von PK-Produkten mit unterschiedlichen Materialhärten und Viskositäten. Eine Auswahl ist in Abbildung 6 dargestellt.
Silikone:
Neben den einkomponentigen Polyurethanen bietet ELANTAS Europe auch einkomponentige Silikone an, die als Dam-and-Fill-Kombination verwendet werden können. Eine Materialkombination, welche auch in Abbildung 7 gezeigt wird, besteht im Bectron® SA 70P1-30 (Dammmaterial) und dem Bectron® SC 76V1-20 (Füllmaterial). Beide Materialien sind kondensationsvernetzend. Bei der Reaktion wird unter Zugang von Luftfeuchtigkeit Methanol als Reaktionsprodukt abgespalten (eine sogenannte alkoxy Vernetzung). Der Vorteil dieser Materialkombination aus Silikonen liegt dabei vor allem in der hohen Temperaturbeständigkeit und der hohen Flexibilität über den gesamten Temperaturanwendungsbereich (-50 bis +200 °C).
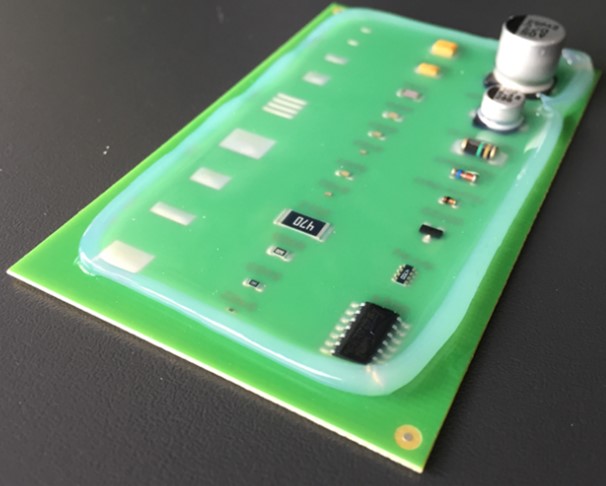
Zusammenfassung
Dam-and-Fill ist ein präziser Prozess, der durch die Kombination eines hochviskosen Dammmaterials und eines niedrigviskosen Füllmaterials den selektiven Schutz von elektronischen Bauteilen auf der Leiterplatte ermöglicht. Der resultierende Dünnschichtverguss bietet einen signifikant besseren Schutz als ein herkömmlicher Dünnschichtlack. Gleichzeitig ist es durch den selektiven Prozess im Vergleich zum Komplettverguss des Bauteiles möglich, das für den Verguss notwendige Gehäuse sowie erhebliche Mengen an Vergussmaterial einzusparen.
Haben wir Ihr Interesse geweckt?
Dann kontaktieren Sie uns gerne unter bectron.elantas.europe@ und erkundigen Sie sich nach einem kostenlosen Muster!. altana. com
Lernen Sie unser Produktportfolio für den Elektronikschutz kennen.
Materials for Electronic Protection (elantas.com)